The end client (DELONG INSTRUMENTS) needed to expand their production capacity with another CNC machine. At the same time, they wanted to upgrade their manufacturing operations and begin a gradual process of automation and robotization. The client's basic requirement was to handle precision workpieces with the utmost finesse.
Customer Profile
DELONG INSTRUMENTS is a Czech company operating since 1992 in the field of electron optics, microtechnologies and nanotechnologies. It supplies low-power transmission electron microscopes (LVEM) and Schottky electron nozzles (DIGUN) to scientists worldwide. Institutional and industrial partners appreciate its unique customized and OEM solutions and tailor-made special components from the first design to the final device.
ADATE is a major supplier of complete CNC technologies for business in the Czech and Slovak Republics.
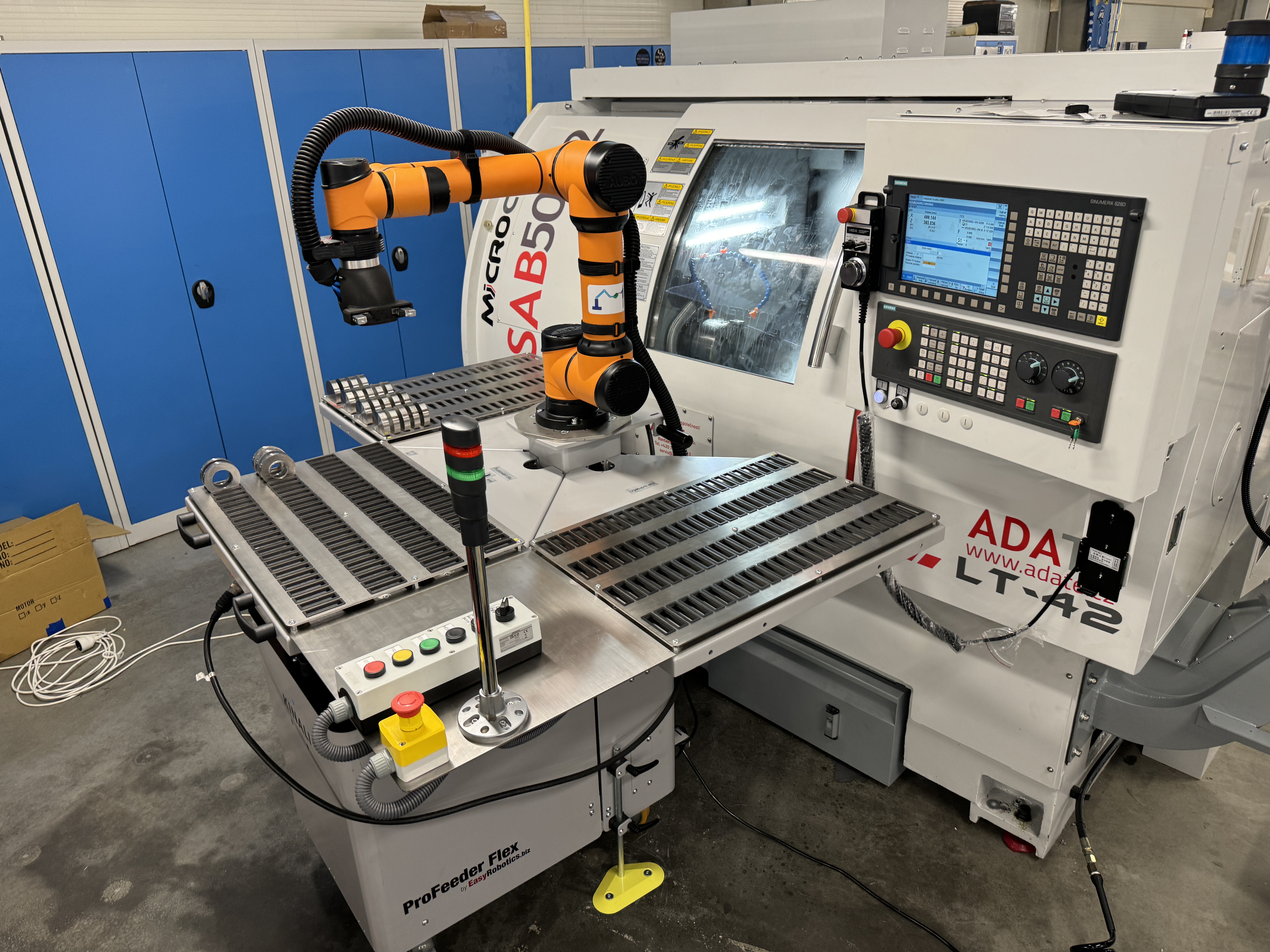
Project brief
In view of the need to increase production capacity, the client requested ADATE to supply a new CNC machine. However, it was to include a robotic workstation for its automated operation.
The client is one of the Czech leaders in metalworking and, as a very successful innovator in the field, is looking for further opportunities to strengthen this position. Despite its specific small batch production, it decided to try automation. Therefore, the request for a robotic workstation went to ADATE.
With this assignment, ADATE then approached our company KINALI, primarily due to our long experience in designing robotic workstations and our own development capabilities for complete HW and SW supply.
The key requirement was to handle the workpiece as delicately as possible, where any damage caused by clumsy robot handling (or, for example, leaving gripper marks) would result in large, and most importantly, unnecessary losses for the client.
The classic CNC feeder was not a suitable solution for this type of implementation. In addition, the client required a modular solution in the form of a collaborative robot that could be easily used at another site if required. This allowed the client to achieve maximum robot utilisation and the best possible return on their investment.
Do you have a similar need as Delong Instruments?
Get in touch. We'll be happy to design a customized solution for you.
Do you have a similar need as Delong Instruments?
Get in touch. We'll be happy to design a customized solution for you.
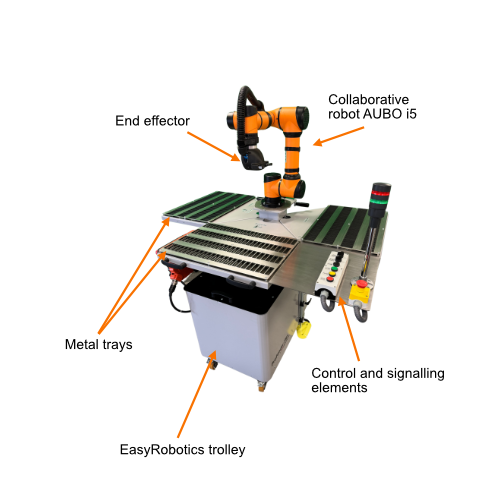
Designed solution
The device is designed as a robotic workstation used to automate the operation of a CNC lathe. It includes three tables with sheet metal racks for inserting parts. These racks form trays for input and output material. Each tray contains 100 positions and is used for storing parts at a specific stage of the operation. The left tray (looking into the CNC machine) is used for storing the input blank, the middle one for storing the blank after the first operation and the right one for storing the output parts.
In principle, the workstation operates by sequentially removing parts from each position and loading them into the lathe after the program has started. It communicates with the lathe and when the operation is complete, the robot blows air to clean the part of excess material, removes it from the clamps in the CNC and places it on the appropriate table. It then inserts the next blank and instructs the CNC to start the operation.
When designing the solution, we considered whether to use the AUBO i10 (with a load capacity of 10 kg) or the i5 (with a load capacity of 5 kg). In the end, we chose the i5 option as its range and weight is sufficient for most of the operations considered by the client and it is cheaper compared to the i10.
The blower used to clean the parts, located on the robot's end effector, is custom-made in KINALI's capabilities (using our own 3D printers).
Thanks to the use of three staging tables, the part can be machined unattended from both sides while the workpiece can be replenished on the fly at the input. This creates a continuous operation.
We were considering a dual gripper that could handle two parts at once for the job. However, this is an additional investment. As the client did not require high speed machine operation and a dual gripper would have unnecessarily increased costs, we dropped this option.
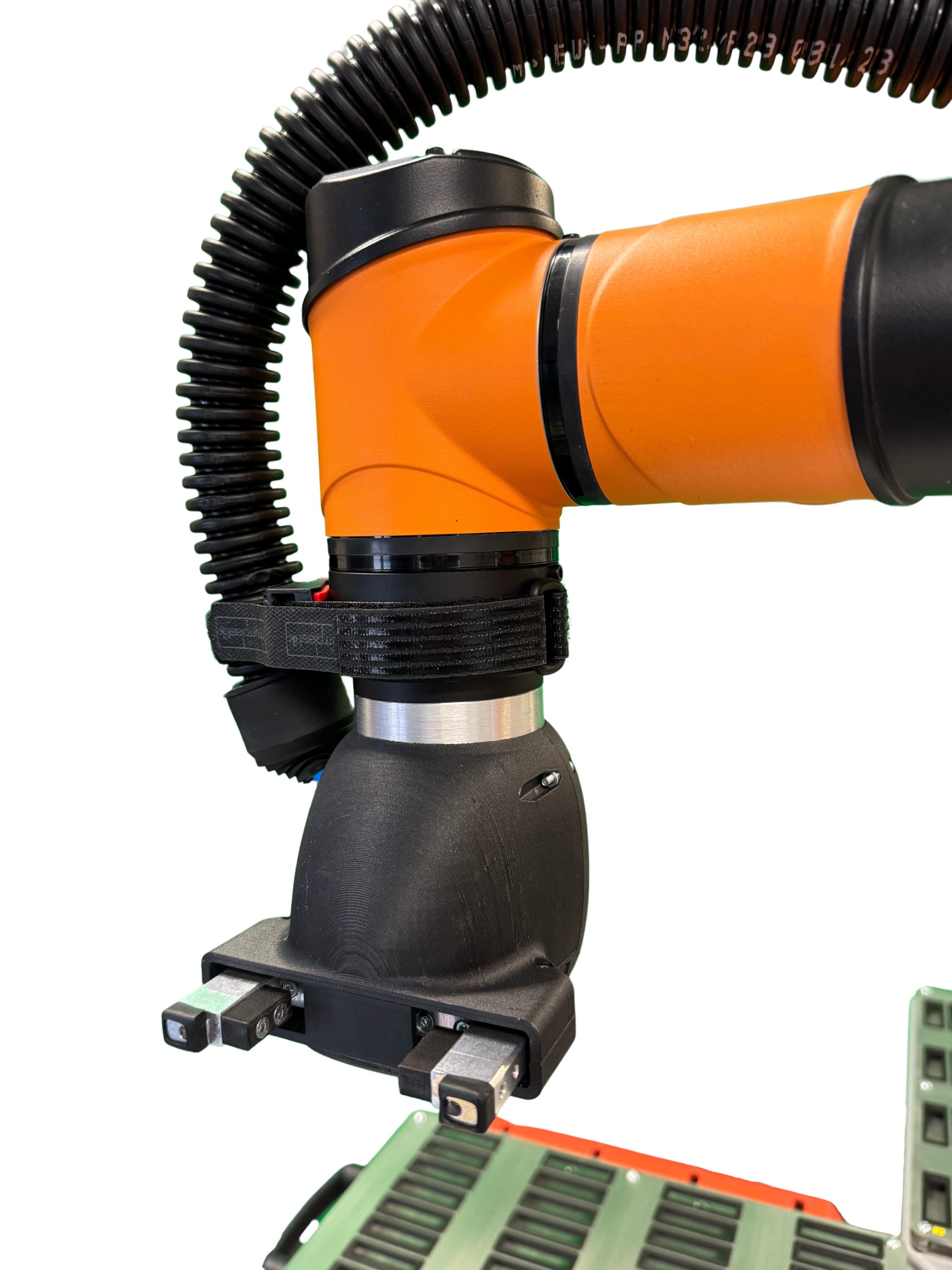
Technical parameters
Robot | AUBO i5 Collaborative Robot |
End tool |
Custom built for the client
|
Robotic base |
ProFeeder Flex from EasyRobotics
|
Workstation control method | Customised button panel, cobot control display (teach pendant) |
Execution
The execution of the contract had a total of four phases, namely:
- design phase (conceptual study, prototype, final design);
- implementation phase (assembly, programming, testing at KINALI premises by in-house QA staff);
- testing at ADATE after connection to CNC;
- final deployment at the client (DELONG INSTRUMENTS).
Output of the solution
The workstation is designed to operate the CNC machine for one entire shift without the need for a human operator. With a hopper for up to 100 pieces of input material, the entire shift is covered from this perspective as well. Simply fill the hopper at the beginning of the shift and dump the finished workpieces at the end of the shift. If necessary, the input material can also be replenished while the machine is running, thus ensuring an essentially endless loop of the entire CNC line.
In addition, by placing the AUBO i5 Collaborative Robot on the EasyRobotics robot base, which allows easy relocation to any place, we have added a truly flexible partner to DELONG INSTRUMENTS' production. It can easily be placed next to any machine and within a few hours, new motion paths and tasks can be configured for it in the intuitive AUBO controller environment or by guiding the robotic arm.
Conclusion
The new challenge for our development team was to design and manufacture a device for cleaning workpieces from splinters and implement it into a single end effector with a gripper. In addition, the gripper was modified so that it could not leave handling marks on the material under any circumstances.
Robotic workstations used to operate CNC machines are among the standard solutions supplied by KINALI to industrial plants. This implementation was atypical by developing a customized end effector that combines a gripper with a blower for cleaning parts using air. At the same time, it is an example of successful cooperation on complex deliveries with other top Czech companies (here ADATE).