The owners of Lemmacon approached us with the need to robotize their production line for the production of plastic packaging, namely shipping crates. The reason for this was a shortage of production staff combined with a desire to streamline production and ensure scalability (to cater to large impact orders where multi-shift operations need to be covered at short notice). Part of the brief was to supply a versatile and modular system so that the client could also use it for other production processes, without the need for significant additional investment.
Client profile
Lemmacon s.r.o. specializes in the development, production, sales and services related to returnable transport packaging, especially for the automotive industry. Thanks to a team of experts with many years of experience, it offers not only a wide portfolio of standard transport packaging, but also the design and production of packaging tailored to the needs of clients.
Lemmacon emphasizes speed and flexibility, which enables it to respond promptly to specific customer requirements. Thanks to its own production capacities and modern technologies, the company is able to realize orders from the design and development of packaging to final delivery within very short deadlines.
Thanks to its cooperation with a number of partners and more than 15 years of experience in the industry, the company is the ideal partner for efficient and high-quality packaging solutions.
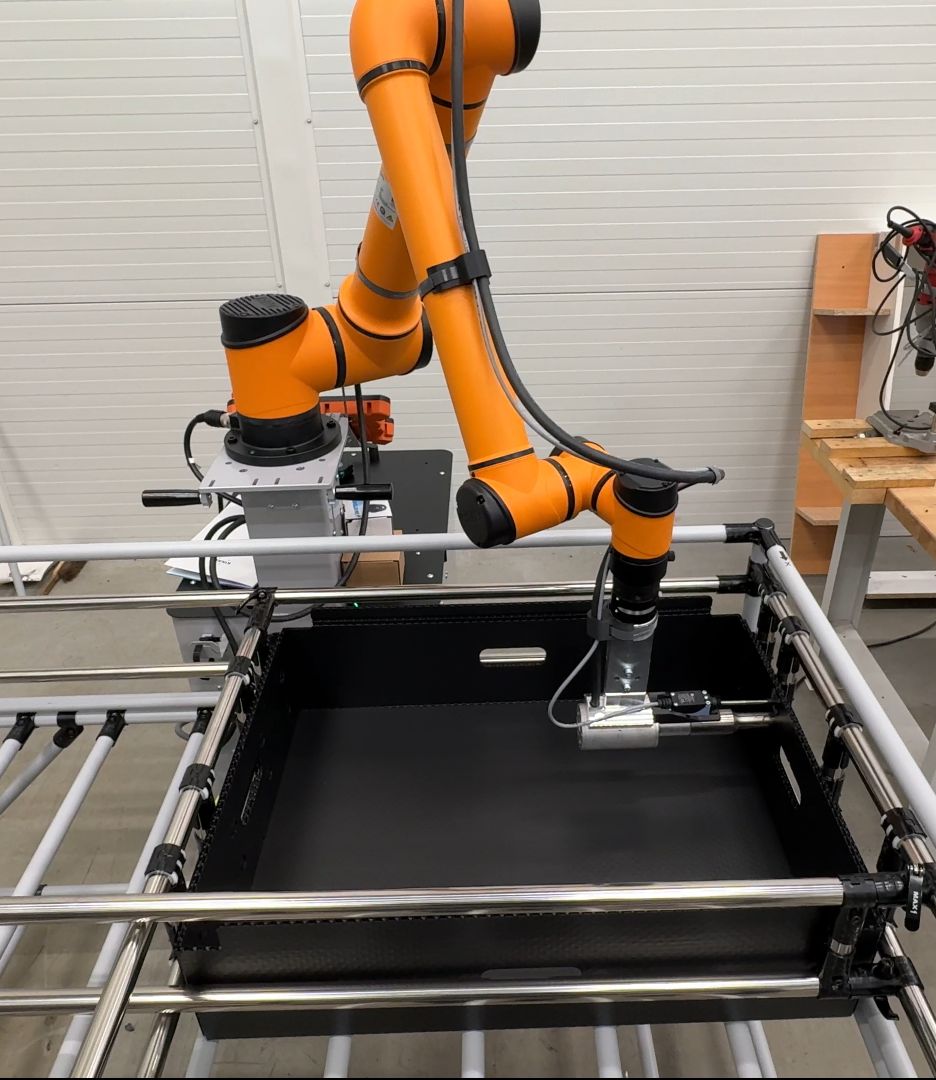
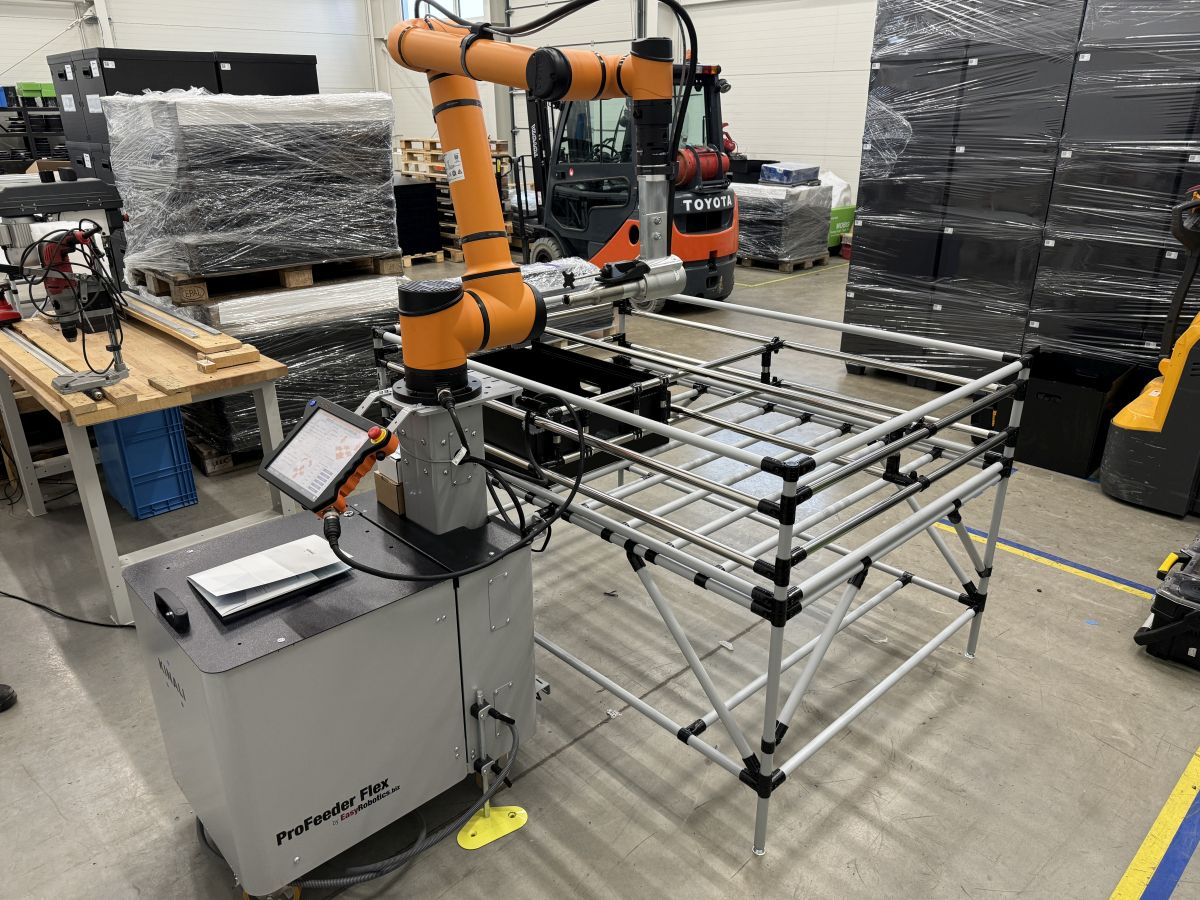
Project assignment
The customer primarily wanted to automate the use of their ultrasonic welding machine for plastic welding using the AUBO collaborative robot. The task was to service a wide product portfolio. In this case, it was packaging material in the form of plastic crates. It was necessary to:
• Control the ultrasonic welder using digital inputs and outputs
• Detect sufficient weld depth to ensure the required strength of the joint
• Prepare the AUBO collaborative robot for a quick change for another application
Proposed solution
The device is designed as a universal robotic workstation used to automate the operation of an ultrasonic welder with space for assembling several pieces of plastic boxes at once. The client had the table for material storage and box assembly custom-made by an external supplier and the KINALI team subsequently integrated it into the robotic workstation.
By combining a collaborative robot, a mobile robot base, and a quick tool change solution, we have delivered a highly versatile system that can be "taught" new tasks in just a couple of hours. It can thus operate a different workstation every week without any problems.
The AUBO collaborative robot in the i10 variant was chosen because of the required reach. This is up to 1,350 mm for the i10. It is currently the second-largest reach in the entire AUBO i product range.
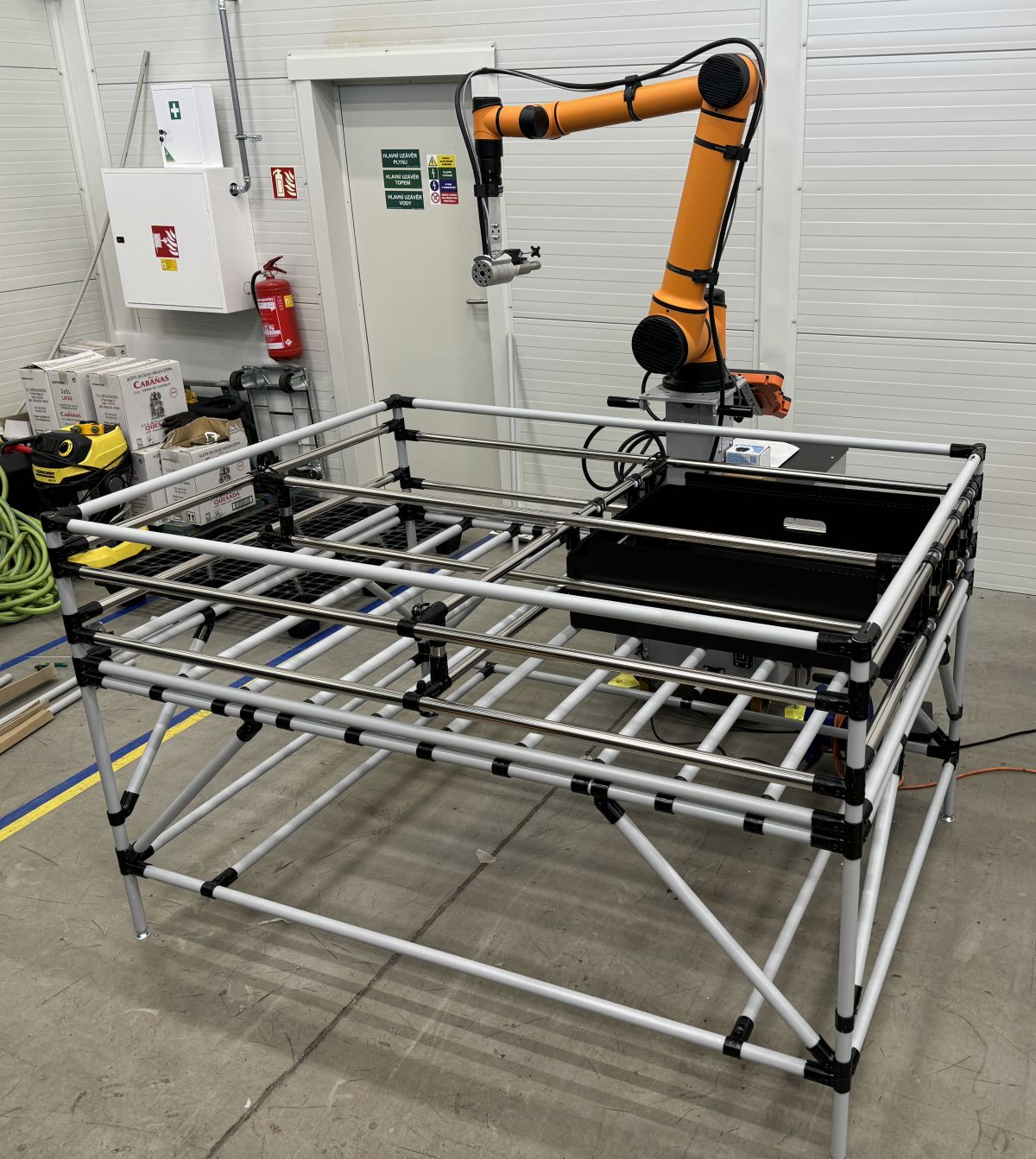
Do you have a similar need as Lemmacon?
Contact us. We will be happy to design a tailor-made solution for you.
Do you have a similar need as Lemmacon?
Contact us. We will be happy to design a tailor-made solution for you.
Technical Parameters
Robot | AUBO i10 collaborative robot |
End tool |
Built to client specifications
|
Robotic base |
ProFeeder Flex from EasyRobotics
|
Method of workplace control | Robotic hand guidance (when "learning" new movements), cobot control display (teach pendant). |
Execution
The implementation of the contract had three phases, namely:
- Design phase (conceptual study, prototype, final design);
- Recovery (assembly, programming, testing in KINALI premises by our own QA staff);
- Final deployment at the client's site and testing in real production conditions (Lemmacon s.r.o.).
Result of the solution
The workplace is designed to ensure unattended production of four pieces of plastic boxes. Subsequently, the assistance of a worker is required to remove the finished products and prepare the material or semi-finished product for the next production cycle.
The ultrasonic welder is attached to the AUBO collaborative robot by a custom-designed and manufactured aluminium bracket. It is equipped with a joint for 90° rotation and long enough to operate even in deep plastic boxes.
There is also a limit switch on the welder holder. It is triggered against the box wall when the maximum weld depth is reached, ending the welding process. The position of the switch can be changed to adjust the desired weld depth.
Lessons learned
The contract necessitated the coordination of multiple suppliers with the client's wishes, thanks to the fact that in addition to our company Kinali, which supplied the robotic system, another supplier contributed to the entire project by supplying a table for assembling the plastic boxes.
Conclusion
Robotic workstations used to operate various production or industrial equipment and machines are among standard solutions supplied by KINALI to industrial plants. This realization was atypical in the development of a customized end effector, which allows automatic control of the ultrasonic welder and at the same time measuring sufficient weld depth to ensure sufficient strength of the manufactured packaging.