Client Profile
Our client is a Czech company specializing in the production and sale of folding rulers and other measuring tools. Their products include wooden folding rulers, colored folding rulers, and classic wooden rulers. These products are available in various sizes and are made from high-quality materials such as hornbeam, birch, and beech. The company’s products are renowned for their high quality and durability, as evidenced by the various certifications they have received.
Project Assignment
The project was driven by the need to fully automate the production of wooden folding rulers. To achieve this, the client invested in a completely new production line. For full automation, it was necessary to replace human workers in the quality control process of the incoming material—specifically, wooden blocks. To ensure material quality, it was essential to inspect the blocks from all sides, both in terms of dimensions and the desired shape, as well as for the presence of undesirable wood defects.
To maximize material yield, the client required that each detected defect be recorded, including its location. This information is then transmitted to the production line, which uses it to optimize material yield and subsequent sorting.
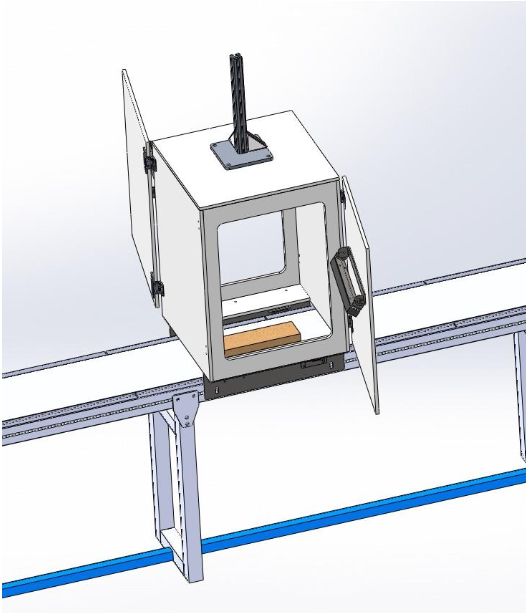
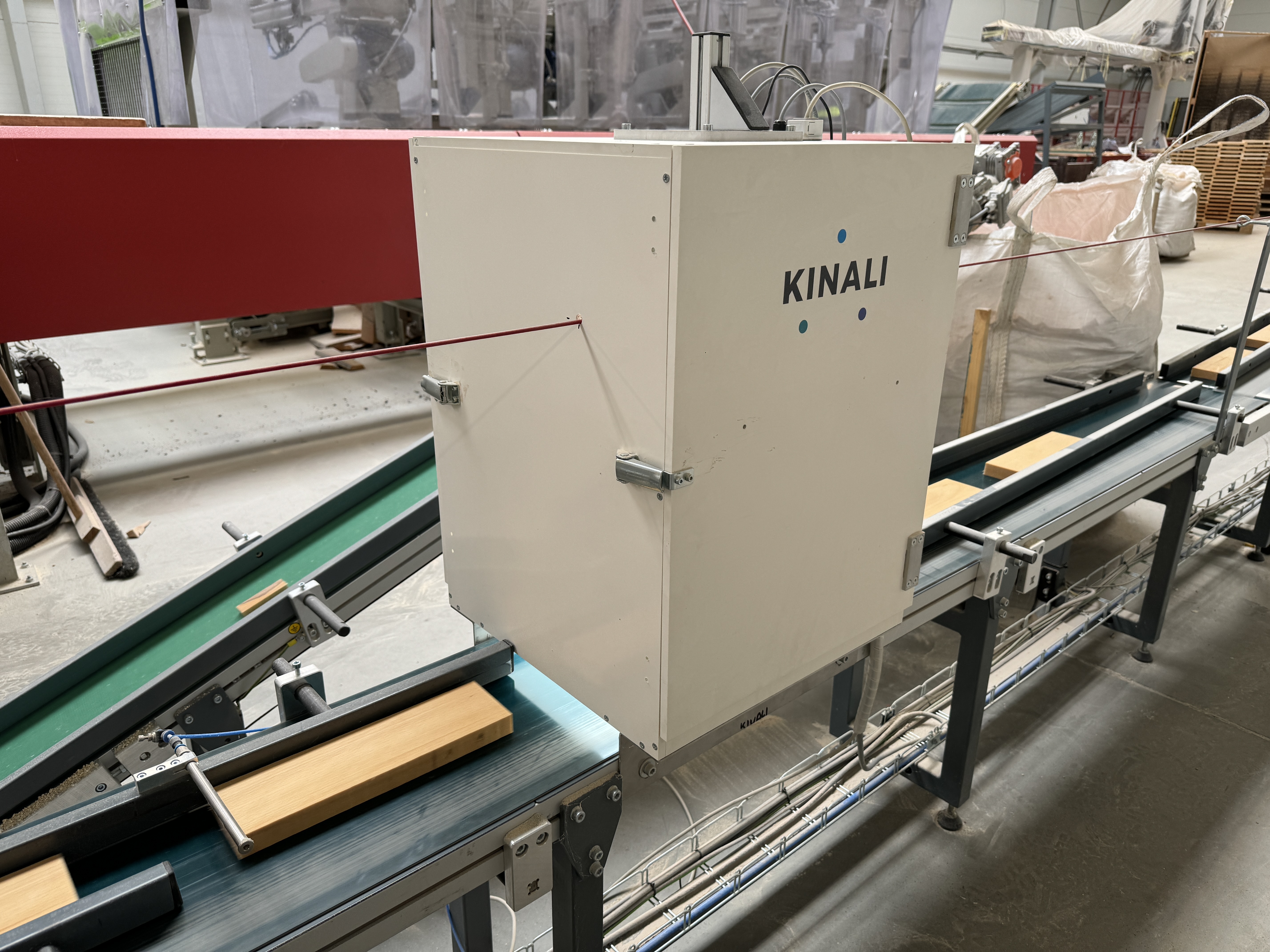
Proposed Solution
After an initial analysis, the KINALI team decided to solve the task by installing two camera cells, which are separated on the production line by a mechanism for rotating the blocks. Each cell inspects the block from the opposite side and independently evaluates the quality and dimensional accuracy of the wood.
We assess the wood quality using a trained AI model capable of classifying the blocks into pre-defined categories. For better shape recognition, the system is equipped with a laser, which is further processed by a detection algorithm.
The software package of the inspection device includes direct communication with the superior production control system, which is continuously updated based on inspection results. The inspection system can operate at a speed of up to 90 blocks per minute, which corresponds to a belt speed of approximately 0.5 m/s.
Our solution is unique in its ability to deliver a complete turnkey camera inspection system. KINALI’s services in this case include problem analysis, solution design, construction of the camera cell, and integration into the existing production line.
The software part of the project includes the development of custom inspection algorithms (if necessary—we do not rely solely on integrating existing smart cameras). This also includes the delivery of a user interface that meets the client’s operational procedures and software integration with other relevant customer production equipment (in the spirit of Industry 4.0).
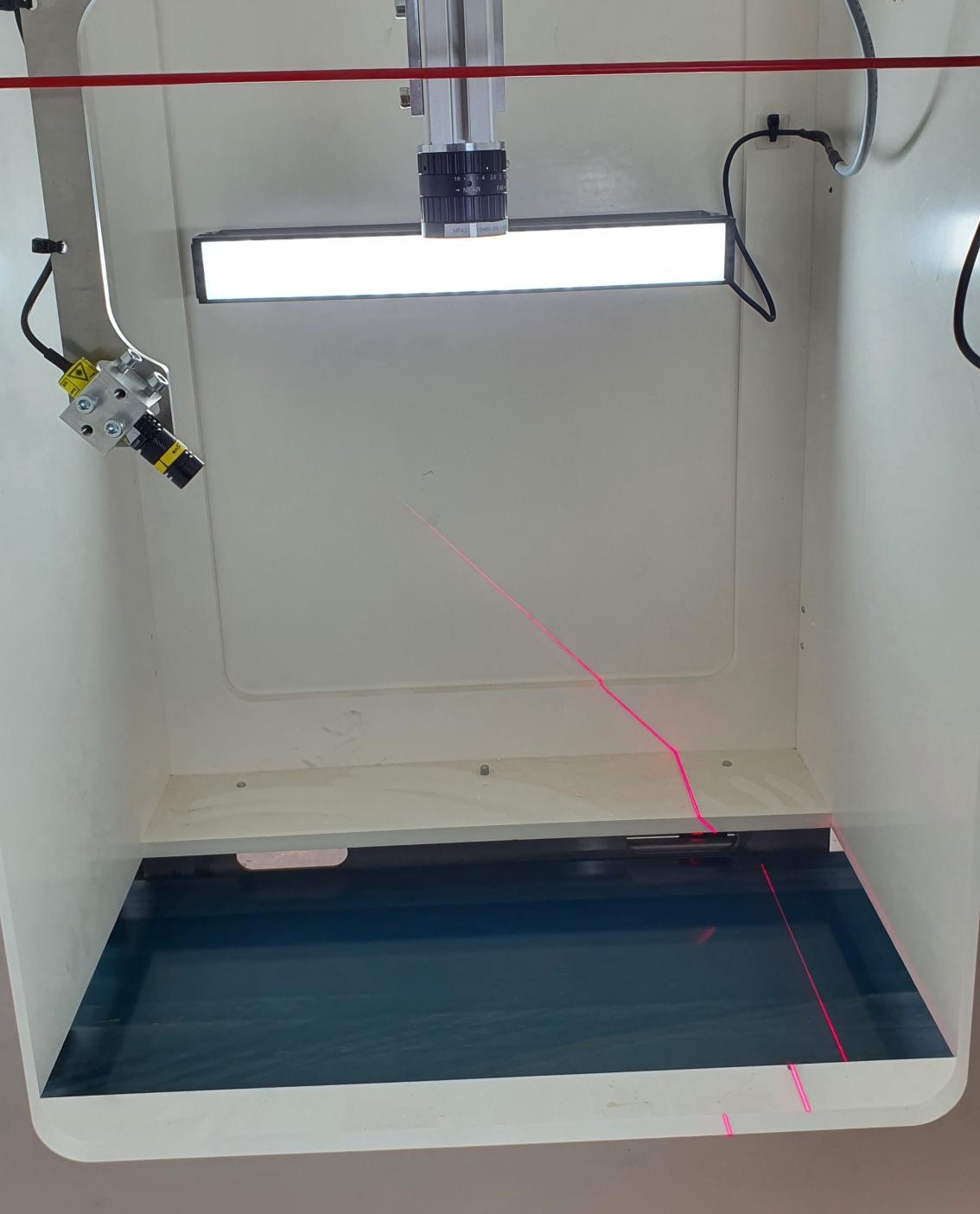
Do you have a similar need as Metrie?
Get in touch. We'll be happy to design a customized solution for you.
Do you have a similar need as Metrie?
Get in touch. We'll be happy to design a customized solution for you.
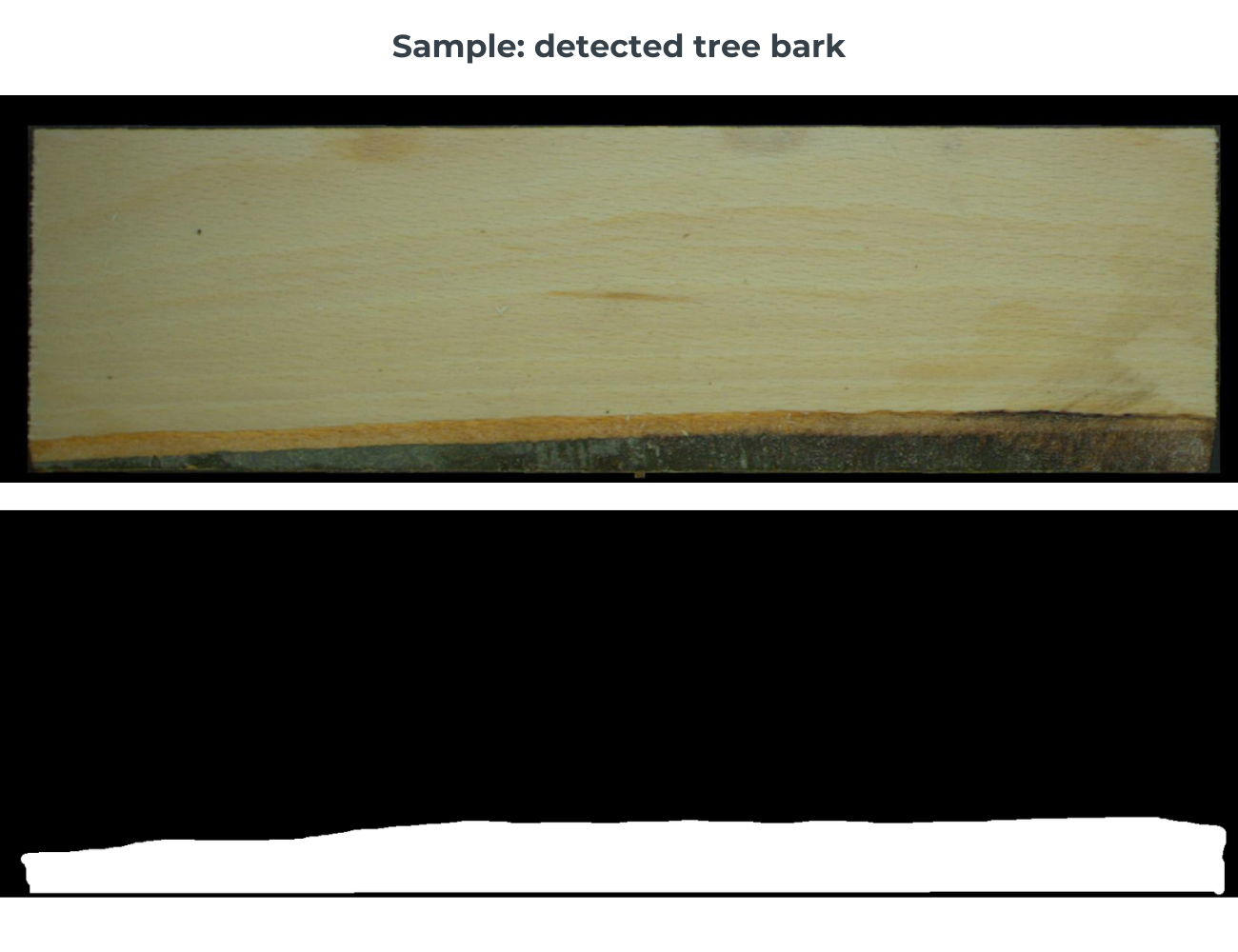
Implementation
The device is designed as an automated workstation for inspecting and measuring wooden blocks and is part of the production line. It consists of two optical inspection stations located above the conveyor and a control cabinet with an industrial computer.
The input to the device is wooden blocks with widths of 85 mm, 65 mm, and 55 mm from a sawmill located near the inspection stations. The supply of these semi-finished products is automated using an industrial conveyor.
The device operates on the principle that after starting the production line, it waits for the input material (blocks). As soon as the first block from the previous part of the line (sawmill) arrives, it enters the first inspection station, where inspection images are taken. These are immediately sent to a neural network, which evaluates defects on the specific piece. The evaluation result is then sent to the evaluation system, displayed in the graphical user interface (GUI), and possibly stored in memory.
After completing the inspection at the first station, the block continues on the conveyor. On its way to the second inspection station, it is rotated top-side down and then undergoes the same inspection as at the first station. The result is also displayed in the graphical user interface (GUI).
In the next step, the results from both inspection stations are summarized and displayed in the appropriate section of the inspection software as the final evaluation of the block and its assignment to a specific quality category.
After evaluation, the block moves further along the conveyor to pneumatic ejectors, which sort the material according to its quality onto adjacent conveyor belts designated for that category.
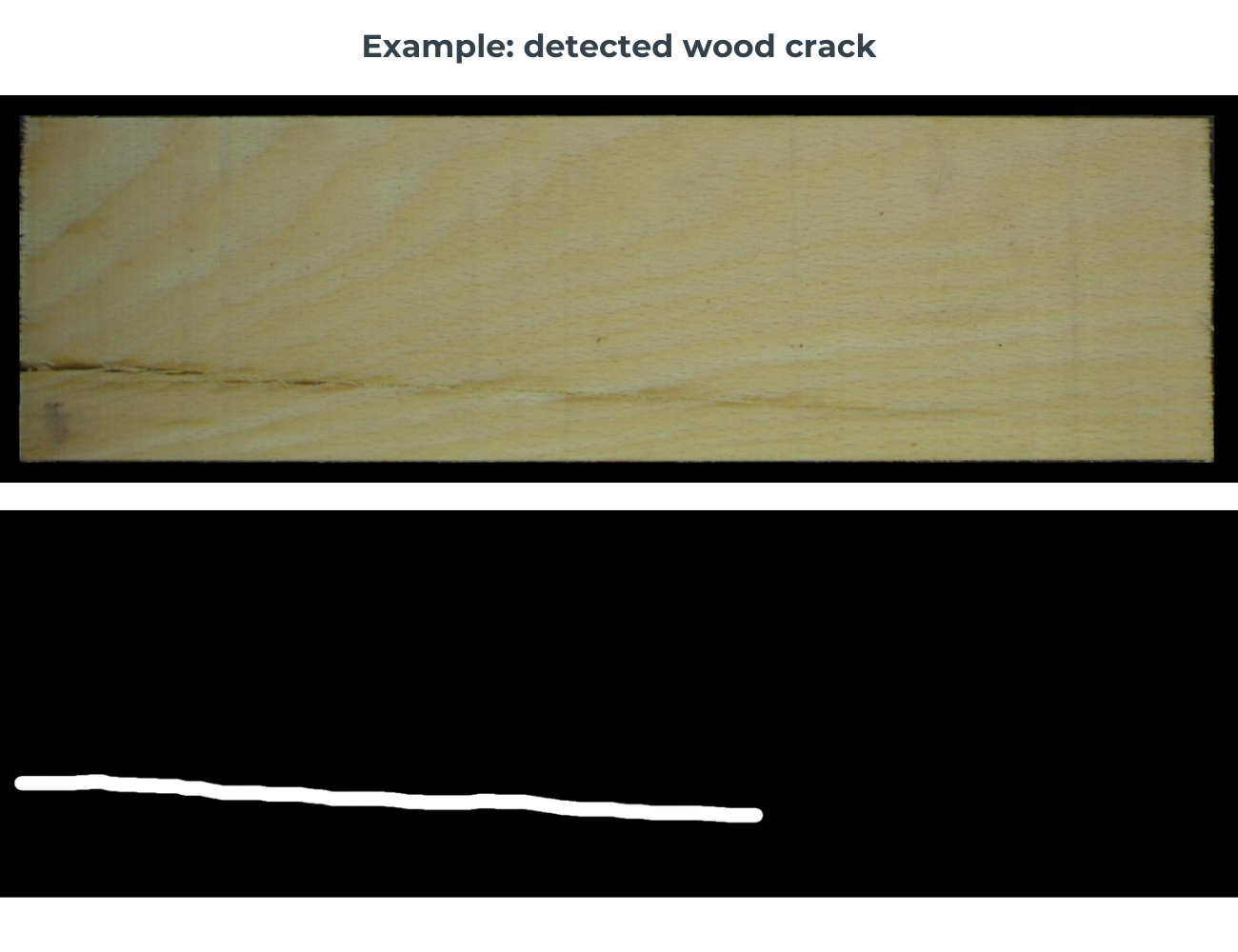
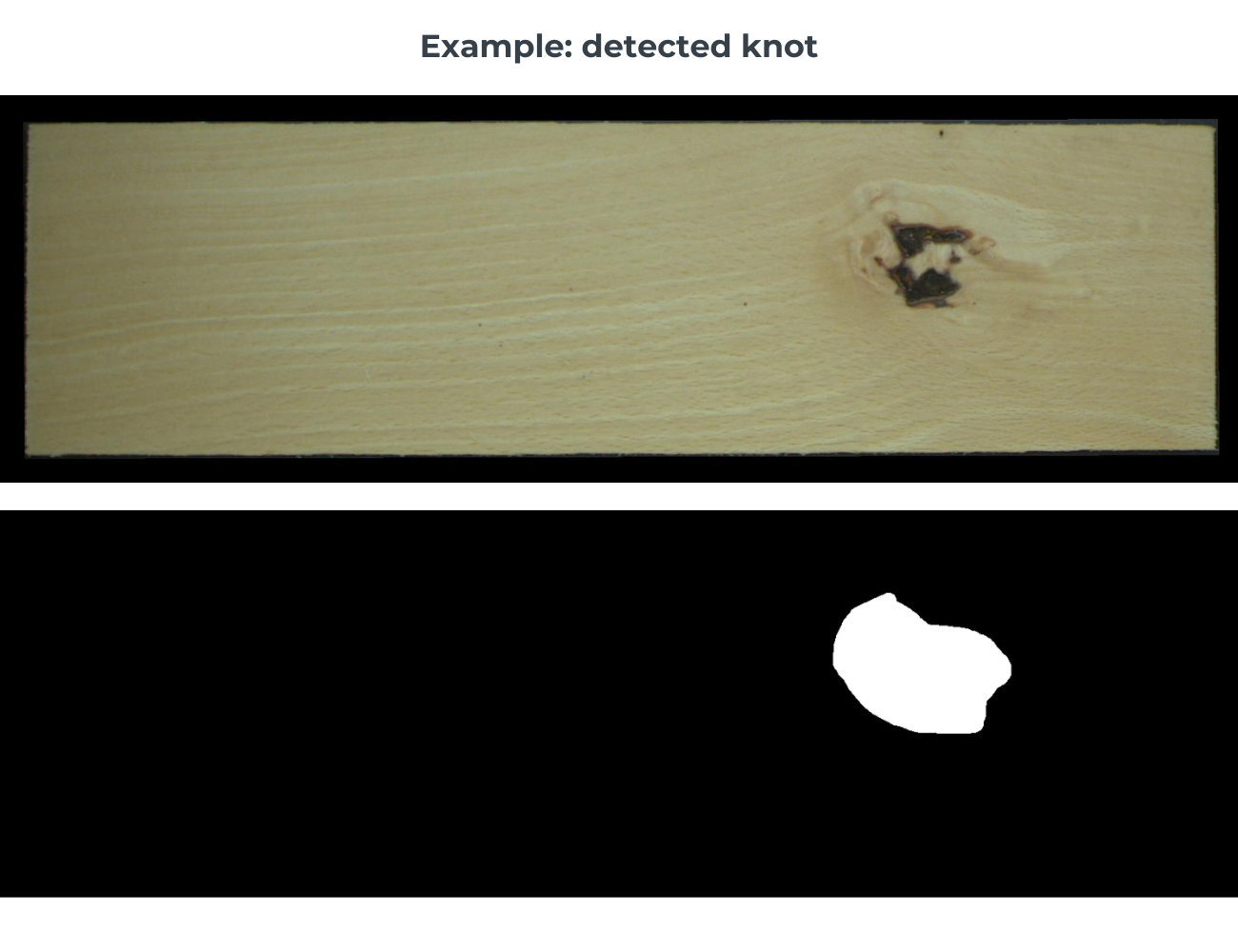
As part of the project, it was necessary to analyze the current state of quality control performed by the client’s inspectors and use this analysis to design new classification rules. It was also necessary to agree on the technical parameters of the new production line with its supplier, such as speed and the communication method between the two production nodes. This was followed by intensive communication with the customer regarding the optimization of defect categorization and the collection of representative samples for each category.
After training the initial AI models and constructing a test device in our laboratories, we began the initial testing phase of the complete solution. Our internal QA department played a significant role in this phase, ensuring the validation of the camera inspection system’s behavior against the project specifications.
After installing the new production lines at the customer’s site, testing moved to the client’s production facilities, where the overall functionality and reliability of the solution from all involved parties were fine-tuned.
Roles Involved from the KINALI Team
- Project Manager
- Software Developer
- AI Engineer
- Mechanical Designer
- Electromechanic
- QA Engineer
Conclusion
The automation project for the optical inspection of wooden blocks for Metrie demonstrated how an effective combination of AI, laser scanning, and camera systems can significantly improve the quality and efficiency of the production process. By deploying two independent camera cells capable of detecting and precisely locating defects on the blocks, we successfully reduced defect rates and optimized material usage.
This project allowed us to expand our capabilities in detecting new wood material defects and working with new types of wood. The challenge lay in combining AI optical inspection with laser scanning of the wooden blocks’ surface shape. Our AI models were further refined and improved in reliability after project delivery. Another challenge was the intensive collaboration with another technology partner who supplied a different part of the production line.